Schwingungen messtechnisch erfassen
Praxiswissen zur Messung und Analyse von Dreh- oder Torsionsschwingungen
Sie betreiben eine Maschine, bei der Sie Drehschwingungen erwarten oder sogar schon beobachtet haben. Erste Modellrechnungen bzw. Messungen am Maschinengehäuse konnten deren charakteristische Frequenzen auf einen ungefähren Bereich eingrenzen. Jetzt möchten Sie diese Schwingungen sauber messtechnisch erfassen und deren Amplituden im Betrieb überwachen. Wir zeigen Ihnen im Folgenden, wie Sie hier effizient vorgehen.
Begriffsklärung: Drehschwingungen oder doch Torsionsschwingungen?
Oftmals werden die Begriffe Drehschwingung und Torsionsschwingung synonym zur Beschreibung desselben Phänomens verwendet: Ein drehbar gelagertes System schwingt um eine seiner Achsen. Ganz allgemein handelt es sich hier also um eine Drehschwingung. Eine Torsionsschwingung bezeichnet nun einen speziellen Typ von Drehschwingung, nämlich einen, bei dem ein Teil der Rotationsenergie der Drehung zyklisch zu einer Verdrillung bzw. Torsion eines Bauteils des schwingenden Systems führt. Da dies in vielen praktisch relevanten Fällen zutrifft, können in der Tat meist beide Begriffe gleichermaßen zur Beschreibung des Phänomens verwendet werden. Je nachdem, ob für eine spezielle Anwendung nun die Torsion oder die Verdrehung von größerer Relevanz ist, wird oftmals eher dem einen oder dem anderen Begriff der Vorzug gegeben. Da die von uns bevorzugte Messmethode die Drehung und nicht die Torsion auswertet, sprechen wir in diesem Artikel von Drehschwingungen.
Messaufbau: Was gehört wohin? Wie heißt was?
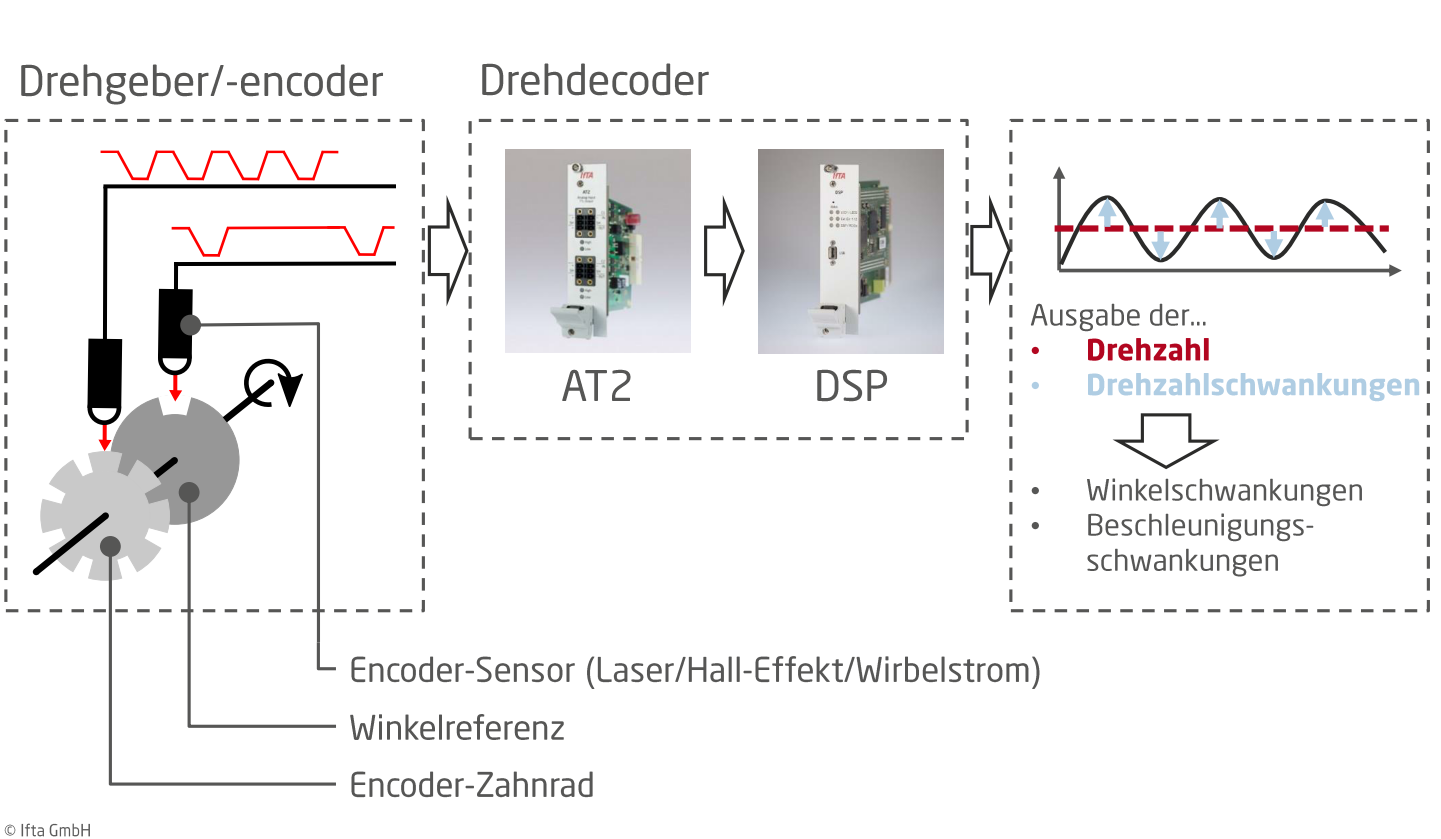
(1) ein Drehgeber bzw. -encoder sowie (2) ein Drehdecoder.
Zur Vermessung von Drehschwingungen benötigt man, wie in Abbildung 1 dargestellt, im Wesentlichen zwei Komponenten: (1) einen Drehgeber bzw. -encoder sowie (2) einen Drehdecoder. Der Drehgeber kodiert die Drehschwingungsinformation in ein spezielles Ausgangssignal, welches vom Drehdecoder dekodiert und in die gewünschte Ausgabegröße (Drehzahl, Winkel-/Drehzahl- bzw. Beschleunigungsschwankungen) umgerechnet wird. Da ein solches System nicht nur den Drehschwingungsanteil, sondern auch die stationäre Drehzahl auswertet, spricht man von einem Tachometer.
Der Drehgeber besteht meist aus einem an der zu vermessenden Welle befestigten Zahnrad, das von einem Abstandssensor, dem Encoder-Sensor, abgetastet wird. Auf diese Weise wird ein Signal erzeugt, das die charakteristische Kontur des Zahnrades – bestehend aus Tälern und Plateaus – abbildet. Jedes dieser Täler/Plateaus definiert ein Trigger-Event. Die zeitliche Abfolge dieser Events codiert dann die Drehzahl- und Winkelinformation. Zur Erzeugung einer Winkelreferenz wird oftmals ein weiteres Zahnrad verwendet, welches nur einen einzelnen Zahn bzw. Nut besitzt und damit einen Nullwinkel definiert. Mit Hilfe dieser beiden Zahnräder lässt sich dann die momentane Position der Welle zu jedem Zeitpunkt eindeutig beschreiben. Alternativ zu einem Zahnrad wird, je nach Anwendung, oft auch sogenanntes Zebratape oder eine Lochscheibe verwendet.
Die vom Drehgeber erzeugten Signale werden zum Drehdecoder geleitet. Bei IfTA-Messsystemen besteht dieser aus dem Timer-Modul AT2 und einem digitalen Signalprozessor (DSP). Das AT2-Modul bestimmt die zeitliche Position der Trigger-Events (Täler/Plateaus) hochgenau und der DSP errechnet basierend darauf die momentane Drehzahl und Drehzahlschwankung (bzw. die gewünschte Ausgabegröße). Einige Systeme unterstützen eine im Decoder integrierte Winkelreferenz, z.B. einen einzelnen breiteren Zahn, womit auf ein dediziertes Zahnrad zur Definition eines Referenzwinkels verzichtet werden kann: Der Messaufbau wird dadurch einfacher und platzsparender.
Sensorwahl: Laser, Hall-Effekt oder doch lieber Wirbelstrom?
Wie oben beschrieben, tastet im Drehgeber ein Abstandssensor ein Zahnrad ab. Abhängig von den Umgebungsbedingungen und Genauigkeitsanforderungen, muss hierfür ein für die jeweilige Anwendung optimaler Sensor gewählt werden. Laserbasierte Sensoren, wie etwa das IfTA-Laser-Tachometer, bieten einen hohen Fokus und Präzision, haben für den rauscharmen Betrieb jedoch relative hohe Anforderungen an die Oberflächenbeschaffenheit des Zahnrades. Zudem können sie nur in sauberen Umgebungen, die frei von Öltröpfchen, Staub, etc. sind, betrieben werden. Sensoren, die auf dem Hall-Effekt oder dem Wirbelstromprinzip beruhen, sind hier unempfindlicher, haben jedoch einen nicht so engen Fokus. Damit können sie scharfe Konturen weniger präzise erkennen, sind aber auch weniger rauschanfällig.
Encoderwahl: Wie finde ich den richtigen?
Nehmen wir an, Sie haben im Rahmen Ihrer Vorabanalyse eine maximale zu erwartende Drehschwingungsfrequenz von 800 Hz ermittelt. Sicherheitshalber möchten Sie daher einen Decoder wählen, der Drehschwingungen bis 1 kHz auswerten kann. Ihre Welle drehe zudem konstant mit 50 Hz. Wie Sie basierend auf dieser Spezifikation einen passenden Drehgeber wählen, zeigen wir Ihnen im Folgenden.
Bevor wir zur konkreten Umsetzung kommen, wollen wir uns noch die hierfür notwendigen Grundlagen erarbeiten. Die grundlegende Einheit des hier vorgestellten Messprinzips entspricht einer vollständigen Umdrehung der zu vermessenden Welle. Aus diesem Grund werden alle Vorgänge gerne auf eine volle Wellenumdrehung bezogen. Dies bedeutet insbesondere, dass Schwingungen nicht mehr in Zyklen pro Zeit (Frequenzbereich), sondern in Zyklen pro Wellenumdrehung (Ordnungsbereich) angegeben werden. Wie in Abbildung 2 dargestellt, besitzt eine Schwingungsform oder Mode der Ordnung 1 genau einen Zyklus pro Umdrehung. Analoges gilt für Schwingungen höherer Frequenz. Um Größen vom Ordnungs- in den Frequenzbereich zu konvertieren, muss folglich mit der Drehzahl multipliziert werden.
Die Encoderauflösung N beschreibt nun, wie viele Trigger-Events pro Umdrehung vom Encoder aufgenommen werden. Im Falle des Zahnrads entspricht sie genau der Anzahl an Zähnen bzw. Nuten. Es ist wichtig zu verstehen, dass die Auflösung im Ordnungsbereich (Trigger-Events pro Umdrehung) einen fixen Wert hat, nämlich N. Im Zeitbereich skaliert sie (Trigger-Events pro Zeit) jedoch mit der Drehzahl, Drehzahl multipliziert mit N. Zeitlich hochfrequente Phänomene lassen sich also nur bei entsprechend hohen Drehzahlen untersuchen. Es ist hierbei immer sicherzustellen, dass die Abtastrate des Analog-Digitalwandlers für das Encoder-Sensor-Signal zur Erkennung aller N-Trigger-Events hinreichend hoch ist (üblicherweise im 100 MHz Bereich).
Genauso wie im Zeitbereich gilt auch im Ordnungsbereich das Nyquist-Shannon-Abtasttheorem: Ein Signal der Ordnung O kann aus einer Folge von äquidistanten Abtastwerten genau dann exakt rekonstruiert werden, wenn es mit einer Encoderauflösung von N > 2 · O abgetastet wurde. In Abbildung 2, rechte Spalte, ist dieses Kriterium für drei verschiedene Modenordnungen beispielhaft ausgewertet. Da sich Drehschwingungen nicht an die grundlegende Einheit des Messprinzips halten, treten sie im Allgemeinen bei einer nicht-ganzzahligen Ordnung auf, also z. B. 3,42. In einem solchen Fall sollte für die Bestimmung der minimalen Encoderauflösung zur nächsten ganzen Zahl aufgerundet werden, hier also 4.
Gerüstet mit diesem Wissen, lassen sich die die Anforderungen an den Drehgeber für obiges Beispiel wie folgt berechnen:
- Eine Schwingung von 1 kHz entspricht bei einer Drehzahl von 50 Hz genau einer Mode der Ordnung O = 1000/50 = 20.
- Nach Nyquist-Shannon wird damit ein Encoder mit einer Auflösung N > 2 · 20 = 40 benötigt.
- In der Praxis hat es sich bewährt, auf diese Zahl nochmal rund 25 Prozent aufzuschlagen. Demnach wäre ein Encoder mit mindestens N = 50 Zähnen/Nuten zu wählen.
Autor
Thomas Steinbacher, Entwicklungsingenieur
Kontakt
IfTA GmbH
Junkersstraße 8
82178 Puchheim
+49 8392 719 84
+49 8392 719 11