Modulares Konzept schafft Platz im Schaltschrank
IP67-Lösung inklusive Safety und I/O-Hubs mit IO-Link unterstützt bei der Modularisierung von Produktionslinien
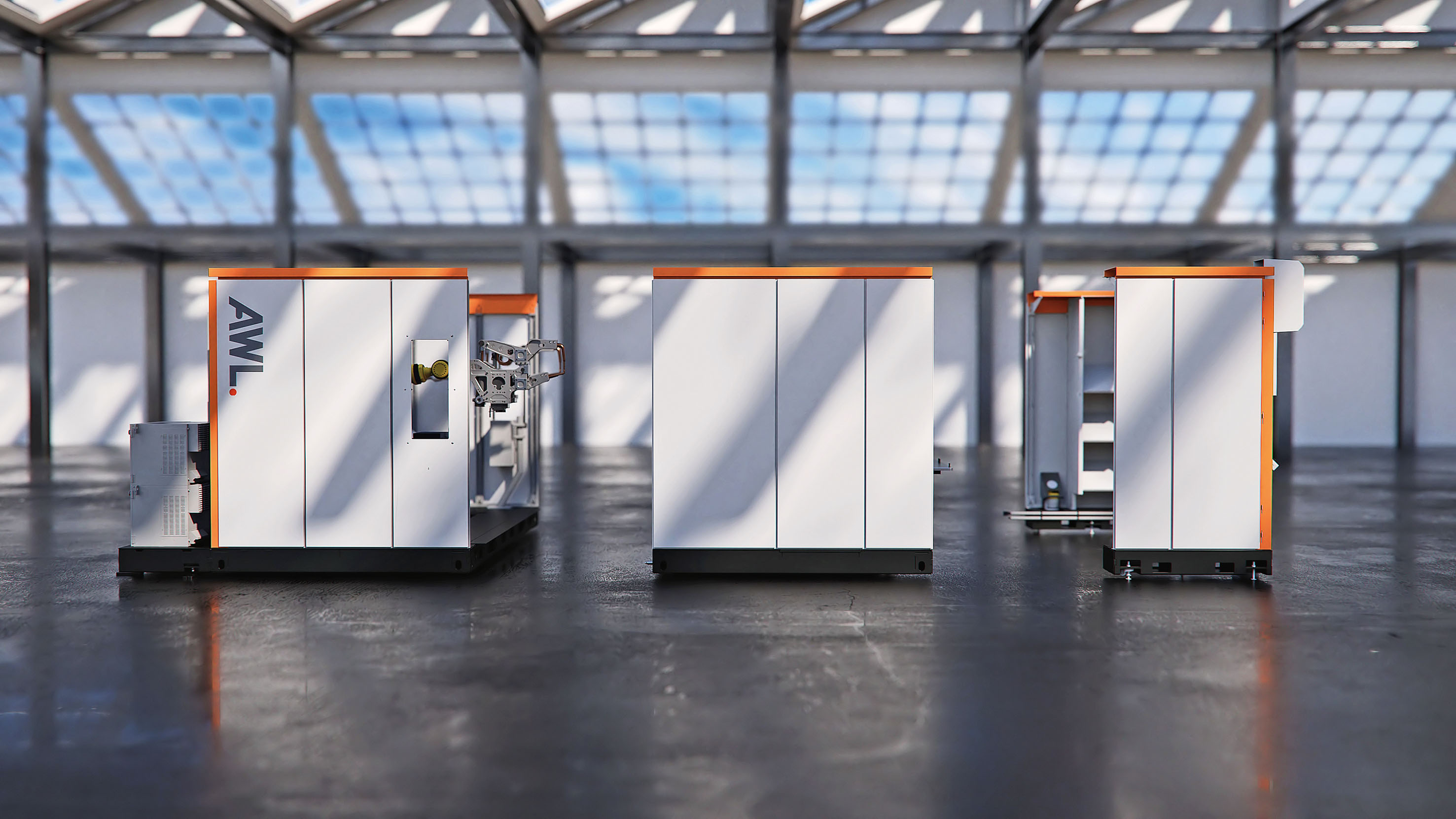
Wer heute eine Küche im Online-Konfigurator zusammenstellt, erlebt Modularität in Reinform. Dabei setzen sich die einzelnen Module wiederum aus Modulen für die Seitenwände, Bodenplatten, Rückwände und Einlegeböden zusammen. Am Ende kann man aus verschiedenen Dekors die Fronten und Blenden wählen, ein Griffdesign sowie eine passende Arbeitsplatte. Am Beispiel der Selbstbauküche wird deutlich, dass Modularität ohne Standardisierung nicht denkbar ist. Erst wenn definierte Abstände, Maße, Bohrungen und Anschlüsse für Wasser oder Gas vorhanden sind, lassen sich die Vorteile einer modularen Produktionsstrategie nutzen: hohe Variantenvielfalt und Flexibilität bei kurzen Durchlauf- beziehungsweise Lieferzeiten und moderaten Preisen.
Mit diesen und weiteren Argumenten überzeugt auch Matthijs Varwijk Interessenten und Anwender vom modularen Maschinenkonzept. Varwijk ist Projekt-Manager R&D und zudem verantwortlich für die Modularisierungsstrategie beim niederländischen Maschinenbauer AWL-Techniek in Harderwijk. Mit mehr als 750 Mitarbeitern an fünf Standorten weltweit hat sich AWL mit seinen automatisierten Schweiß- und Verbindungsstrecken vor allem in der Automobilbranche einen Namen gemacht.
Ein interdisziplinäres Team um Varwijk stellte 2017 das Maschinenportfolio von AWL auf Modularität um und legte nach und nach die Standards der M-Line fest. Dabei musste er zunächst auch intern Überzeugungsarbeit leisten. Gerade in der Übergangsphase vom klassischen zum modularen Produktionslayout sind die Vorteile nicht immer deutlich erkennbar. Zunächst müssen Standards definiert werden, was oft auch mit Einschränkungen verbunden ist.
Den ersten Standard setzte AWL mit dem Namen der Produktreihe: Die M-Line steht einerseits für eine modulare Produktreihe, andererseits verbildlicht der Begriff Line auch die Produktionslinie, zu der die einzelnen Module zusammengesetzt werden. Die Basis jedes Moduls bildet ein Stahlrahmenquader, der so bemessen ist, dass er in einen ISO-Container passt. Das spart Zeit und Kosten bei Transport und Inbetriebnahme der Maschine. Der Anwender kann die Anlage später auch einfach erweitern oder umbauen, da die Module mit entsprechend ausgelegten Staplern wieder neu in der Produktionshalle arrangiert werden können.
Modularisierung braucht Standards
Mit dem Basisrahmen wurden drei zentrale Modultypen definiert, aus denen die M-Line zusammengesetzt werden soll: ein Operator-Modul, in dem ein Werker Bauteile einlegen und Prozesse starten kann, ein Indexer-Modul, das Drehtische oder andere Vorrichtungen zum Handling der Werkstücke umfasst, und ein Prozessmodul, das Werkstücke zum Beispiel mit Schweißrobotern oder anderen Werkzeugen bearbeitet.
Zugute kommt AWL dabei Turcks Ethernet-Multiprotokoll-Technologie für I/O-Module. Sie erlaubt es dem Hersteller, in jedem Modul seiner M-Line identische I/O-Blockmodule einzusetzen – egal ob der Nutzer eine Profinet- oder Ethernet/IP-Steuerung bevorzugt. „Wir wollten so viele standardisierte Komponenten wie möglich, und auch einen weitgehend standardisierten Schaltschrank. Im Idealfall haben wir eines Tages nur noch eine PLC und ein Netzgerät im Schaltschrank“, so Hardware-Ingenieur Jasper van Kooij. So weit ist man heute noch nicht, aber im Schaltschrank der AWL-Module ist bereits viel Luft ist. Dazu tragen auch Turcks IP67-I/O-Hybridkomponenten für Standard- und Safety-Signale bei.
Galvanische Trennung der Sensor-/Aktorspannung
Turcks Konzept einer modularen IP67-IO-Link-Safety-Lösung überzeugte AWL: Den Kern der Lösung bildet das hybride Safety-I/O-Modul TBPN. Das Modul hat einen integrierten Sicherheits-Controller, der Profisafe über Profinet zur Steuerung spricht. Das Modul verfügt jeweils über vier sichere I/Os, zwei klassische digitale I/Os und zwei IO-Link-Ports. An einem der sicheren I/Os ist die Safety-Abschaltbox TBSB angeschlossen, die im Ernstfall die Aktorspannung V2 sicher abschaltet.
Die Spannungsversorgung für alle Module läuft ebenfalls über die Safety-Abschaltbox. So ist sichergestellt, dass beispielsweise bei einem Not-Halt kein Aktor mehr versorgt ist und sich nichts mehr in der Maschine bewegen kann. Die Sensorik bleibt aktiv, da sie über V1 versorgt wird. So ist die Maschine in der Steuerung immer sichtbar. Die digitale Sensorik und Aktorik der Schweißkappenfräser ist an I/O-Hubs angeschlossen, die wiederum mit Turcks IO-Link-Master TBEN-L-8IOL kommunizieren. Der IP67-Block stellt vier IO-Link-Ports nach dem Class-A- und vier nach dem Class-B-Standard bereit. Letzterer trennt die Spannung für Sensorik (V1) von der Aktorik (V2). So kann auch über IO-Link die Stromzufuhr sicher abgeschaltet werden. In ähnlichen Projekten in den USA setzte AWL bereits Turcks TBIP-Modul ein. Es ist hardwareseitig baugleich mit dem TBPN, jedoch für Ethernet/IP und CIP-Safety-Kommunikation ausgelegt.
„Andere Hersteller haben auch Module, die angeblich V1 und V2 getrennt haben. Aber wenn man sich das genau anschaut, ist es nicht konsequent und V1 und V2 teilen sich zum Beispiel den Minuspol“, merkt van Kooij an. Die geteilte Erde kann im Fall eines Kurzschlusses fatal sein. Ein einfacher Isolationsfehler reicht dann, um die gesamte Sicherheitslösung auszuhebeln – einer der Gründe für das konsequent galvanisch getrennte System. „Das komplette Angebot und konsequent getrennte V1- und V2-Kreise konnte uns nur Turck bieten.“
IO-Link stärkt Standardisierung
Durch den Einsatz der IP67-Lösung inklusive Safety und I/O-Hubs mit IO-Link spart AWL viel Verdrahtungsarbeit. Die Verteiler übertragen als IO-Link Device digitale Signale von Aktoren und Sensoren im IO-Link-Protokoll und bringen sie zum IO-Link Master, von wo sie per Ethernet zur Steuerung gelangen. Ein weiterer Grund war für van Kooij und Varwijk, dass die bidirektionale Schnittstelle die Standardisierung der M-Line befeuert. Die sichere Signalübertragung über Dreidrahtleitungen macht viele speziell geschirmte Leitungstypen und Spezialkabel überflüssig. IO-Link sorgt auch für eine höhere Verfügbarkeit der Maschine: Teil der M-Line ist das Dashboard-System Lyla. Es sammelt Daten von verschiedenen Maschinen, wertet sie aus und überwacht so Funktion und Leistung der Maschine. Möglich wird das auch durch die Diagnosedaten über IO-Link.
Die Modularisierung der Steuerungsebene steht noch aus. Hier muss bislang noch jedes Steuerungsprojekt neu aufgesetzt werden, lediglich Funktionsbausteine lassen sich wiederverwenden. Das Modularisierungsprojekt ist aber ohnehin nie abgeschlossen. AWLs Kunden nehmen die M-Line bereits sehr gut an. Einen großen Vorteil sehen sie in der Skalierbarkeit der Maschinen. Es ist kein Problem, ein Operator-Modul später durch eine automatisierte Lösung zu ersetzen, um den Ausstoß zu erhöhen. Das ist wie bei den Küchen: Beim Umzug nimmt man die Küche einfach mit und ergänzt ein paar Module.
Autor
Michael Flesch, Produktmanager Safety-Systeme
Alle Bilder ©Hans Turck
Konzept der zentralen Sicherheitsabschaltung
Das Konzept der dezentralen Sicherheitsabschaltung basiert auf der Idee, im Sicherheitsfall nicht die Spannung jedes Aktors einzeln abzuschalten, sondern in Gruppen von Aktoren. So spart man kostspielige sichere Ausgänge, denn pro Gruppe ist dazu nur ein sicherer Ausgang nötig. Damit nicht alle Sensoren und Aktoren einer Gruppe spannungsfrei geschaltet werden, müssen die I/O-Komponenten die Versorgungsspannung der Sensoren (V1) von der Versorgung der Aktoren (V2) trennen. Die Aktorspannung kann dann sicher abgeschaltet werden. Wie bei klassischer Sicherheitstechnik kann die Sensorik, die über V1 gespeist wird, nach einem Not-Aus weiterhin Signale senden. Mit Turcks dezentraler Abschaltbox TBSB in IP65 ist das Konzept nun erstmalig auch im Feld außerhalb eines Schaltschranks verfügbar.
Kontakt
Hans Turck GmbH & Co. KG
Witzlebenstr. 7
45472 Mülheim an der Ruhr
Deutschland
+49 208 4952-0
+49 208 4952-264