‘MADE-3D’: multimaterial components from a 3D printer
23.03.2023 - 6.7 million euros of funding – Paderborn University is leading a Europe-wide research project.
The next stage of development in the field of metal 3D printing lies in producing multi-material components, in which two or more materials can be arbitrarily allocated as desired. A Europe-wide research team headed by Paderborn University is now seeking to develop industrial applications for this revolutionary technology. Additive manufacturing using multiple materials with different physical properties should take industrial opportunities to the next level. The aim is to enable an unprecedented level of design freedom for highly complex (lightweight) components. To achieve this, the project team is developing innovative multi-material components with locally tailored mechanical, electrical, thermal and magnetic properties for use in the automotive and aerospace industries.
Multi-Material Design using 3D Printing (MADE-3D) – as the project is called – has received around 6.7 million euros of funding for the next three and a half years as part of the European Union’s Horizon Europe 2022 programme. The consortium, consisting of research institutions, additive manufacturing market leaders, the aerospace industry, automotive engineering and start-ups, offers a wide range of international expertise: alongside Paderborn University, the project partners are SLM Solutions, the Fraunhofer Institute for Casting, Composite and Processing Technology IGCV (all three from Germany), the University of the Aegean (Greece), F3nice (Italy), Exponential Technologies (Latvia), QuesTek Europe (Sweden), AVL List (Austria), Skyrora (UK), Safran Additive Manufacturing Campus, the French Alternative Energies and Atomic Energy Commission CEA (both from France), Amires (Czech Republic) and the Swiss Center for Electronics and Microtechnology CSEM (Switzerland).
“Multi-material manufacturing using 3D printing is still in its infancy. The lack of material combinations is the biggest challenge preventing a breakthrough for this technology. ‘MADE-3D’ should offer a leap forward in this regard,” emphasizes project coordinator professor Thomas Tröster, head of the Automotive Lightweight Design (LiA) research group and chair of the Institute for Lightweight Design with Hybrid Systems (ILH) and the Paderborn Institute for Additive Fabrication (PIAF) at Paderborn University.
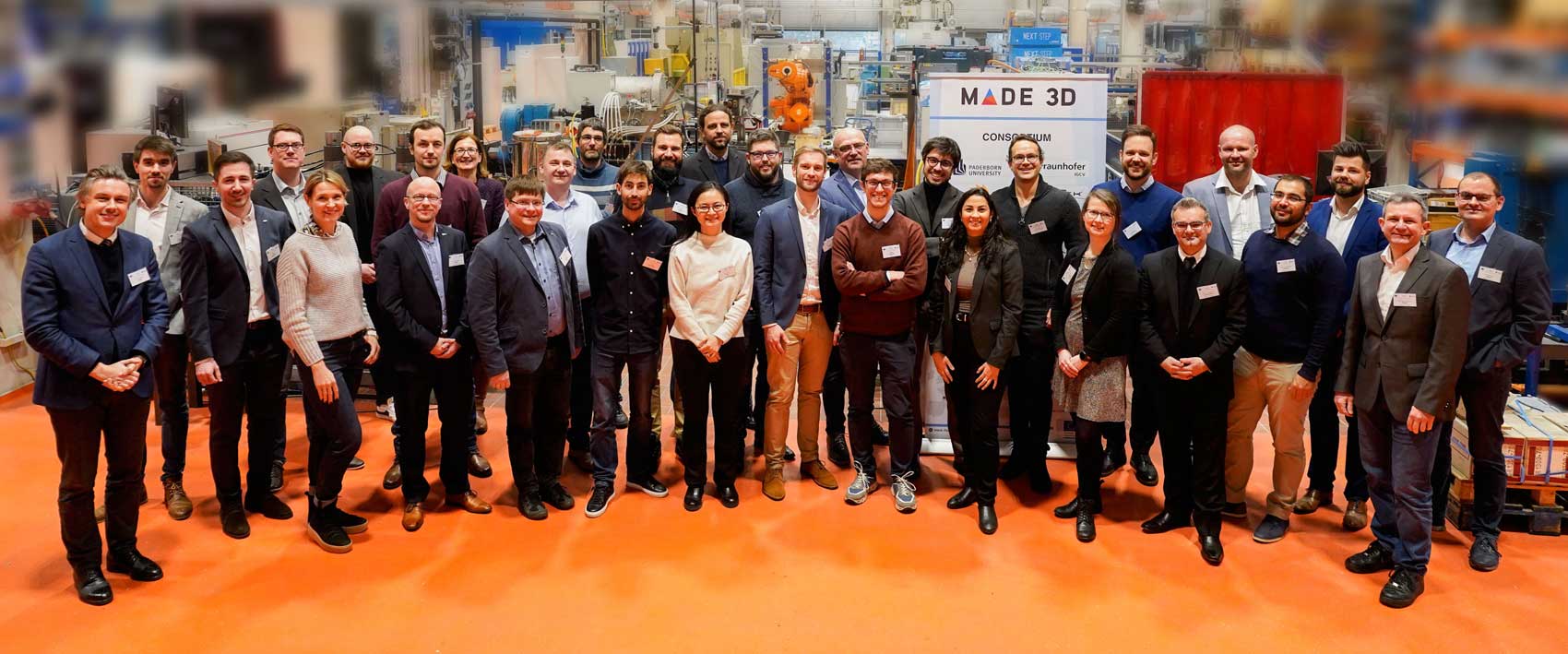
Although additive manufacturing now enables components to be customized to a virtually limitless extent and various functions to be integrated into a single printing process, this requires suitable materials. However, the homogeneous material properties imply that they are insufficient to meet the complex requirements – including flexibility, temperature stability and magnetic properties. Furthermore, the majority of steels and alloys cannot be printed due to cracking. This problem is even more pronounced if two or more materials are combined in an additive process.
This is where the international team of experts comes in. They are seeking to work together to substantially increase the performance of multimaterial components and significantly reduce their weight in order to create new opportunities for lightweight construction. “Our goal is to use the project’s findings to achieve better process reliability and speed in multimaterial additive manufacturing and thus further industrialize this innovative technology,” underscores professor Mirko Schaper, chair of materials science at Paderborn University and project co-leader.
The project team is testing innovative approaches in five areas of application within the automotive and aerospace industries. The objectives for this have been clearly defined: printed multi-materials should reduce the weight of individual parts by up to fifty percent compared with the components currently used – by replacing materials (using lighter metals) and making them using AM (i.e. lower material consumption and customizable functions). Specifically, the areas they are working on include designing lighter drive systems for aviation, in order to save costs and make significant progress in sustainability. They also want to optimize the performance of electric motors by using suitable material combinations, which enable better magnet placement and orientation of the magnetic flow. The project results should ultimately be transferable to numerous other sectors, such as health and energy.
Contact
Universität Paderborn
Warburger Str. 100
33098 Paderborn
Germany
+49 5251 60-0