Easy to install torque measurement without soldering and gluing
Manner Sensortelemetrie
It is particularly suitable as a retrofit due to the short installation time in existing systems. In contrast to the classic strain gauge bonding technology with quasi clean room conditions, TelMAX Torque can be assembled in a short time even under the harshest environmental conditions. The time factor for the installation often plays a decisive role. Adhesive and adhesive curing times for strain gauges lead to long downtimes, which should be avoided. Long layovers are undesirable. Another challenge in the field of measurement technology for larger machines is the transport of the shaft parts and the application capability on site without large transports. TelMAX Torque should offer an alternative solution to conventional sensor and telemetry applications, particularly in the area of large machines, agriculture and cardan shafts for trucks and construction machinery.
The System
TelMA torsion sensor:
The application of the miniaturized telemetric TelMA torque sensor with integrated temperature measurement can be implemented within three minutes. Using micro-welding technology, the finished telemetric torsion sensor is applied without any wiring or gluing. The system works with both one and two sensor elements. Automatic bending moment compensation is activated by using two sensor elements.
The integrated torque measuring cells (torsion sensor) with contactless signal transmission are simply welded onto the shaft body. The torsion sensor technology used in the rotors is based on DMS technology. The telemetry interface with antenna is integrated in the torsion sensor element. This means that the element is completely battery-free and maintenance-free after welding. The high signal sampling rate of 2,000 samples/second guarantees a high signal resolution kHz. This means that dynamic torque signals can also be recorded without any problems.
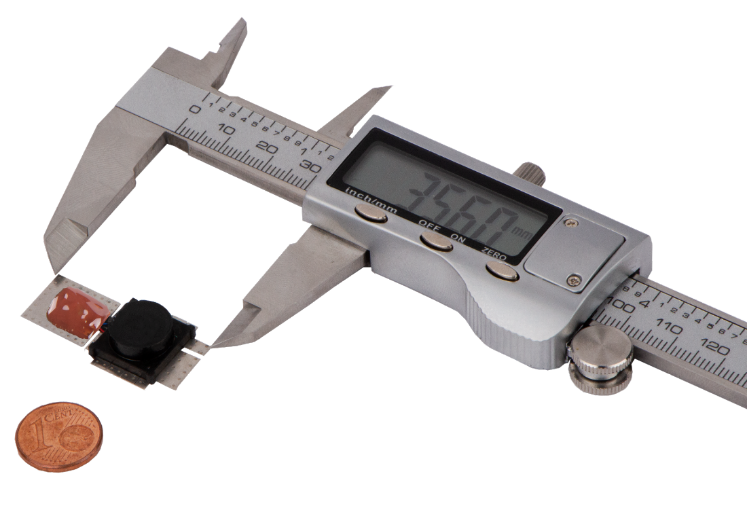
Antenna system:
To pick up the telemetry data at a distance of up to 30 mm, an antenna carrier with integrated copper wire and an intelligent adjustment module is stretched onto the shaft. This antenna support made of plastic or 3D printing can have any diameter from 30 mm ... 1,000 mm. After inserting the copper track, the wire can simply be screwed on.
Stator evaluation unit:
The final component of the system is the robust IP67 evaluation unit with integrated stator antenna. The evaluation unit transmits energy and data inductively via an air gap between the rotating shaft and the supply unit of up to 30 mm. The system's supply voltage of 9-30 V also offers flexibility in use, e.g. in vehicle operation. In addition to the usual 0-5 V voltage output, a current output (4...20 mA) is also available. The additional CAN interface also allows direct signal transmission. The system can be used directly and, if necessary, configured (sensor name, sample rate, information storage, etc.) and calibrated (zero point and gain settings) using the Manner “Telemetry Interface” software.
Contact
Manner Sensortelemetrie
Eschenwasen 20
78549 Spaichingen
+49 7424 9329 0
+49 7424 9329 29